The Ultimate Guide To Alcast Company
The Ultimate Guide To Alcast Company
Blog Article
Things about Alcast Company
Table of ContentsFacts About Alcast Company UncoveredAlcast Company Things To Know Before You Get ThisThe Ultimate Guide To Alcast CompanyThe smart Trick of Alcast Company That Nobody is DiscussingOur Alcast Company DiariesAlcast Company - The Facts
Chemical Comparison of Cast Light weight aluminum Alloys Silicon promotes castability by lowering the alloy's melting temperature level and improving fluidness during casting. In addition, silicon adds to the alloy's strength and use resistance, making it valuable in applications where resilience is crucial, such as automobile components and engine components.It likewise enhances the machinability of the alloy, making it much easier to process right into completed products. By doing this, iron adds to the overall workability of light weight aluminum alloys. Copper boosts electric conductivity, making it beneficial in electric applications. It additionally enhances rust resistance and contributes to the alloy's overall stamina.
Manganese adds to the strength of light weight aluminum alloys and boosts workability. Magnesium is a light-weight aspect that offers stamina and influence resistance to light weight aluminum alloys.
7 Easy Facts About Alcast Company Shown
Zinc improves the castability of aluminum alloys and aids regulate the solidification process during spreading. It boosts the alloy's strength and hardness.
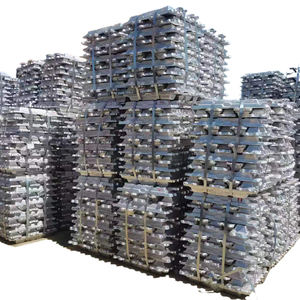
The main thermal conductivity, tensile stamina, yield toughness, and elongation vary. Among the above alloys, A356 has the greatest thermal conductivity, and A380 and ADC12 have the lowest.
The 5-Second Trick For Alcast Company
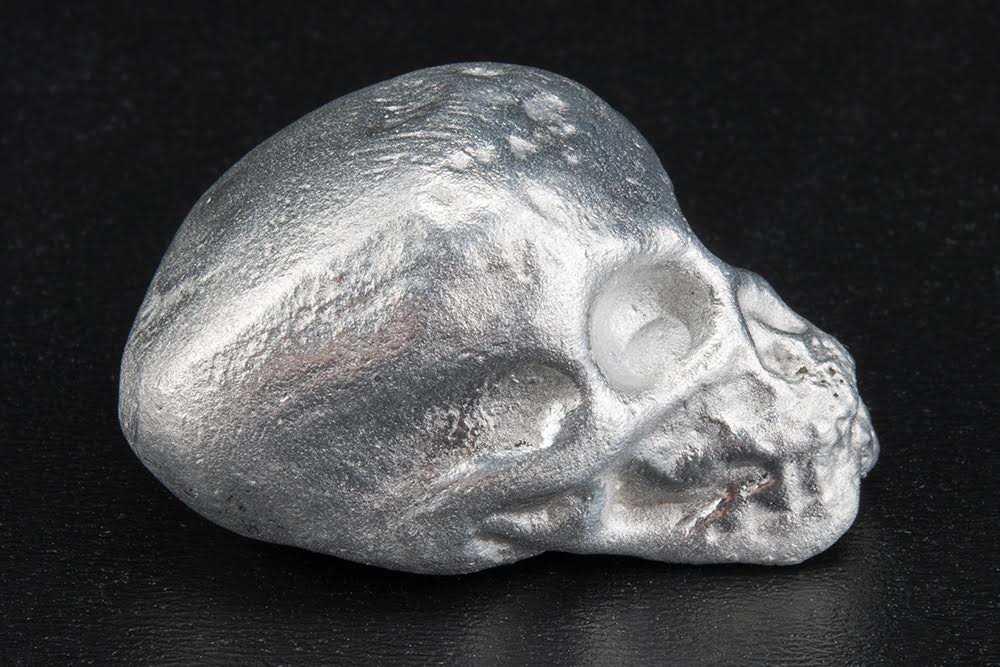
Its special buildings make A360 a beneficial choice for precision spreading in these sectors, enhancing item resilience and high quality. Light weight aluminum alloy 380, or A380, is a widely used spreading alloy with several distinct qualities. It supplies excellent castability, making it a perfect selection for accuracy spreading. A380 shows good fluidity when molten, making certain intricate and detailed mold and mildews are accurately recreated.
In precision spreading, light weight aluminum 413 radiates in the Customer Electronics and Power Devices industries. It's generally utilized to craft detailed parts like smartphone housings, video camera bodies, and power tool housings. Its accuracy is remarkable, with limited tolerances approximately 0.01 mm, ensuring remarkable product setting up. This alloy's remarkable deterioration resistance makes it a superb choice for outdoor applications, making certain lasting, sturdy products in the mentioned sectors.
Everything about Alcast Company
The aluminum alloy you choose will considerably impact both the spreading procedure and the residential properties of the last item. Due to the fact that of this, you need to make your choice carefully and take an educated method.
Identifying one aluminum casting manufacturer of the most suitable aluminum alloy for your application will indicate evaluating a broad variety of attributes. These relative alloy features follow the North American Pass Away Spreading Association's guidelines, and we've split them right into 2 groups. The first category addresses alloy qualities that affect the production procedure. The 2nd covers qualities impacting the buildings of the end product.
The 10-Second Trick For Alcast Company
The alloy you pick for die casting straight influences several aspects of the spreading process, like just how very easy the alloy is to deal with and if it is susceptible to casting problems. Warm cracking, likewise referred to as solidification cracking, is a common die spreading flaw for light weight aluminum alloys that can lead to inner or surface-level splits or fractures.
Particular aluminum alloys are a lot more at risk to hot cracking than others, and your selection needs to consider this. It can harm both the cast and the die, so you ought to look for alloys with high anti-soldering residential or commercial properties.
Deterioration resistance, which is currently a significant feature of aluminum, can differ substantially from alloy to alloy and is an important characteristic to take into consideration depending upon the ecological conditions your product will certainly be revealed to (aluminum metal casting). Put on resistance is an additional building frequently sought in aluminum products and can differentiate some alloys
Report this page